What You Must Know About Machine Guarding Training
- trevorjonesnfu1
- Feb 15, 2023
- 2 min read
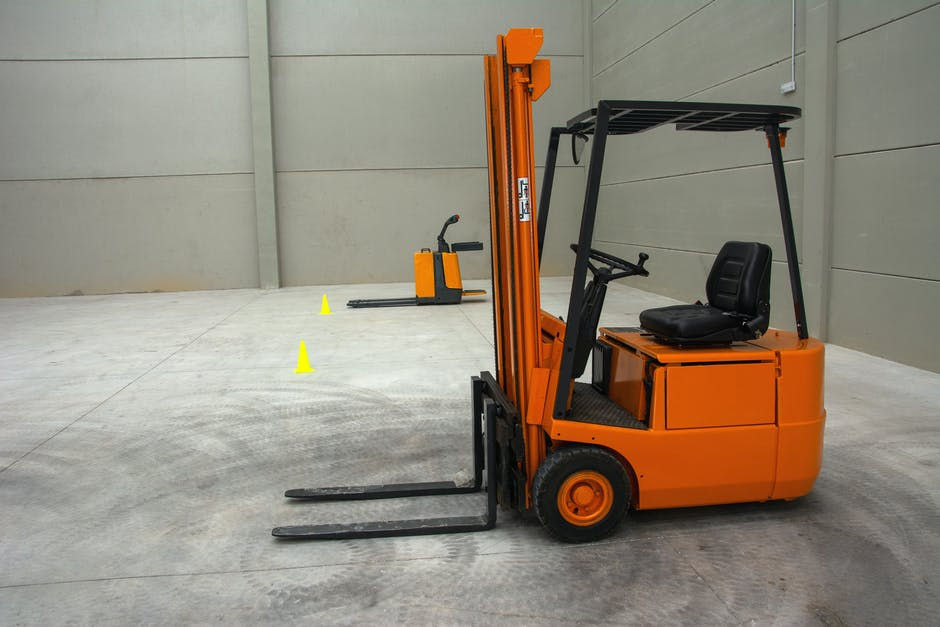
Machine guarding training provides employees with a wide variety of safety skills and knowledge that they can use in the workplace. It also helps them avoid accidents and injuries that can be caused by the presence of dangerous machinery in the workplace.
The first thing that you must know about machine guarding is that it's the process of preventing contact between a worker and a hazardous piece of equipment in the workplace. This is done by using barriers or devices that are installed around the machine and its perimeter, ensuring that workers cannot access the danger area without being properly protected. Helpful resources on the safety skills of workers
Guards and other protective devices can be fixed, adjustable, or self-adjusting and are typically made of metal materials that can withstand impact and prolonged use. Some guards are designed and installed by the machine producer, while others are user-built and can be customized to the specific needs of each machine.
These safeguards are used to protect the operator and other people in the work area from hazardous substances, particles, energy, and even moving parts of the machines that they operate. The most common methods of machine guarding are:
Physical Barriers
A physical barrier is the most basic type of guard and is usually constructed out of solid metal or polycarbonate sheets. These can be welded, screwed or fastened together to form a solid shield that covers the machine. They can also take the form of pressure sensitive mats and light curtains that are placed over an area where the machine is operated. This page will help a worker know all the safety rights required when working in a company.
Other types of protective devices include:
Presence-Sensing Devices
These are mechanical devices that alert the operator if their hands are near the point of operation hazard. The operator is then required to remove their hands from the hazard and perform other actions to avoid the danger. Some of these devices are also able to prevent the operator from entering a hazard area by limiting the amount of time that they can operate the machine.
Another type of device is a pullback or restraint strap that forces the operator's hands to remain outside of the point of operation hazard. These devices are often used in conjunction with other protection systems such as two-hand controls that require the operator to hold down the switch in order for the machine to operate.
The most effective machine guarding is the combination of these different types of safeguards. For example, if an automated piece of equipment like a robotic arm is operating a hazard in the workplace, it must be covered by a safety curtain that can withstand high impact and corrosive elements.
Other methods of protecting the machine and its surrounding areas from hazards are:
Location or Distance Safeguards
These are physical barriers that prevent the hazard from being within 7 feet of a workstation where an operator is working. The materials that these are constructed from vary, depending on the hazard and the location of the hazard. They can be made of metal, plastic or wood, and can withstand impact. For more information, check out this related post: https://www.britannica.com/topic/employee-training.
Comentários